Step into our machine shop and witness the carefully orchestrated processes that drive productivity and ensure the delivery of top-quality remanufactured heads for engines. Join us and our highly qualified personnel, as we take you on a journey through a typical day, where safety, precision, and meticulous attention to detail shape the success of our operations.
Morning JSA and Small Team Meeting:
The day begins with a crucial morning Job Safety Analysis (JSA) session, involving the teams from both the Machine Shop and the MERF (Mesa Engine Rebuild Facility) team Safety takes precedence as potential hazards and concerns are discussed to create a safe working environment. Following the JSA, the small team gathers to align goals and expectations, fostering effective communication and maximizing productivity for the day ahead.
Rotating Stations and Disassembly:
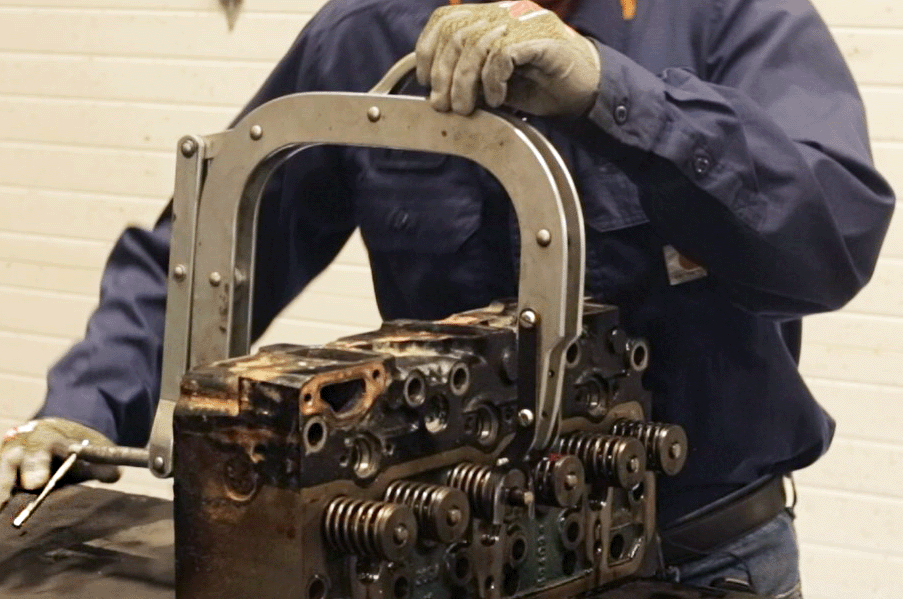
Cleaning and Inspection:
After disassembly, technicians transport the heads to the cleaning bench and meticulously eliminate dirt, grime, and carbon build-up. They subject the heads to a thorough cleaning process, ensuring the elimination of contaminants that could compromise performance. During this phase, technicians conduct detailed inspections, meticulously scrutinizing each head for imperfections that could impact the quality of the remanufactured product. By identifying and addressing issues early on, they maintain a high standard of quality.
Parts Washer and Ultra Sonic Cleaning:
Following the cleaning bench, heads progress to the parts washer. Next, a specialized chemical solution is used to eliminate any remaining paint, dirt, and carbon deposits, leaving the heads pristine and ready for further inspection and restoration. To achieve an exceptional level of cleanliness, heads undergo the ultra-sonic cleaning process. Through the use of high-frequency sound waves, carbon, paint, calcium, and coolant build-up are effectively dissolved, ensuring a deep and comprehensive cleansing of both interior and exterior surfaces.
Rust Inhibitor Treatment and Prep Table:
To safeguard against rusting after complete stripping, technicians subject the heads to a rust inhibitor treatment. This step effectively protects the heads, preserving their durability and longevity. Skilled technicians at the prep table meticulously inspect the heads, taking precise thickness measurements, conducting bolt hole checks, and installing new valve guides, seats, and plugs. These meticulous inspections and installations play a crucial role in maintaining the integrity of the remanufactured heads.
Resurfacing and Debur Process:
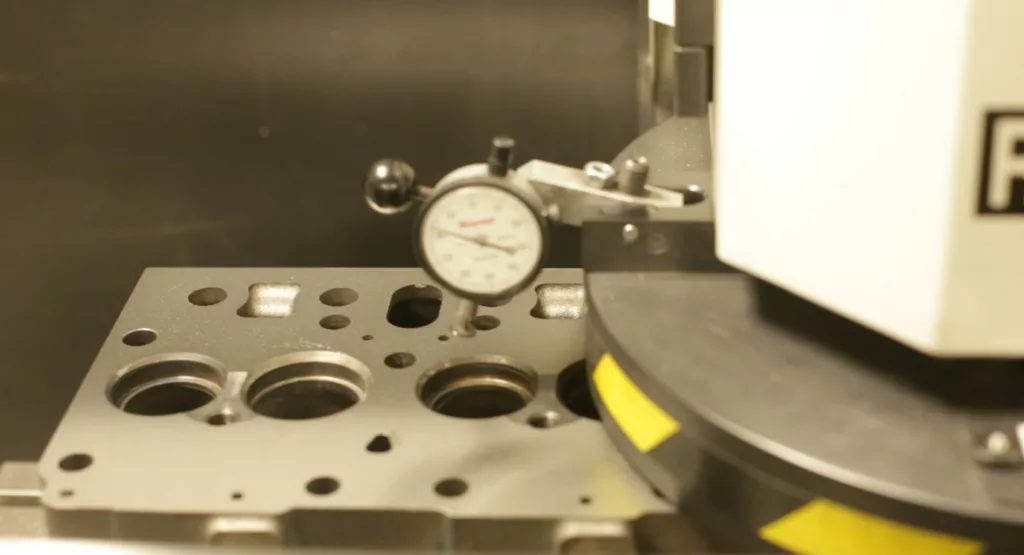
Technicians place the heads onto specialized machines at the resurfacing station, ensuring a smooth and flat surface. This step rectifies any damage or irregularities, ultimately leading to optimal performance and a proper seal upon installation. After resurfacing, technicians meticulously undertake a deburring process to eliminate rough edges and burrs. This meticulous step guarantees a perfect fit and removes any obstructions that could compromise the gasket sealant during installation. Technicians recheck the head thickness, reaffirming their commitment to precision.
Valve Seat Cutting and Vacuum Testing:
Skilled technicians perform valve seat cutting with utmost care and precision. This critical step aims to achieve optimal valve drop height and sealant, ensuring excellent cylinder compression. The integrity of the valves is then verified through vacuum testing, confirming their effectiveness. This rigorous examination reinforces customer confidence in the remanufactured heads and ensures they meet stringent quality standards.
Comprehensive Documentation and Assembly:
Throughout the day, detailed documentation captures each step, measurement, and the responsible team member’s name. This meticulous record-keeping allows for traceability and quality control. The heads move to the assembly station, where experienced technicians skillfully bring all components together. Correctness, cleanliness, and defect-free perfection are diligently ensured during the assembly process. Each component is meticulously installed, following precise procedures and guidelines.
Final Inspection, Stamped Mark, and Packaging:
A dedicated quality control team conducts a final inspection on the assembled heads. They meticulously examine each head, ensuring correctness, cleanliness, and overall quality. Only the heads that meet rigorous standards pass this final inspection. Upon approval, the team stamps each head with a mark indicating the month and year of remanufacturing, symbolizing the commitment to quality and customer satisfaction. With utmost care, they meticulously package the heads for shipment, protecting them during transportation and preparing them for installation in engines worldwide.
Conclusion:
In our machine shop, we prioritize productivity and quality above all else. Through meticulous processes, unwavering attention to detail, and a strong commitment to safety, we guarantee top-quality remanufactured heads. We maintain checklists to track every task performed on each head, ensuring adherence to set parameters. From disassembly and cleaning to precise machining and careful assembly, every step is executed with precision. By strictly following procedures and fostering a culture of excellence, we consistently deliver exceptional remanufactured heads to our valued customers.